In any warehouse or storage facility, space is more than just square footage—it’s an opportunity for efficiency, safety, and scalability.
That’s why warehouse racking plays such a critical role in modern logistics and inventory management.
Whether you’re running a small fulfillment center or a high-volume distribution hub, the right racking system can transform how your business operates.
In this article, we’ll explore the importance of warehouse racking, the different types available, and how to choose a system that aligns with your operational needs.
Table of Contents
What Is Warehouse Racking?
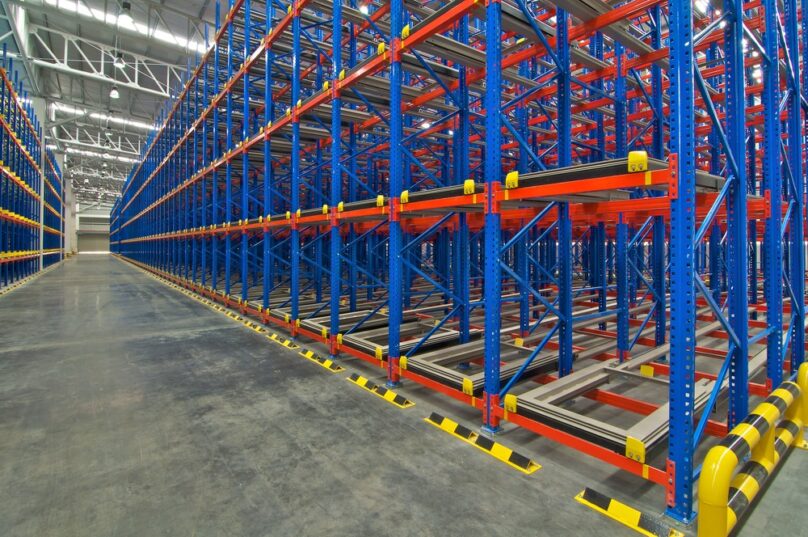
Warehouse racking refers to a structured system made up of shelves, beams, and upright frames designed for storing goods in a systematic and efficient manner.
These systems are engineered to support pallets or containers and allow inventory to be stacked vertically.
Maximizing vertical space is critical for improving storage capacity, especially in environments where floor area is limited or costly.
Proper racking creates a clear layout for warehouses, facilitating better inventory control, faster material handling, and a cleaner working environment.
Without it, stock becomes hard to manage, prone to damage, and difficult to access, slowing down operations and raising safety risks.
Racking systems form the backbone of a productive warehouse.
Their strategic design ensures that materials can be safely and quickly stored or retrieved, which supports higher throughput and lower operational delays.
Why Warehouse Racking Matters
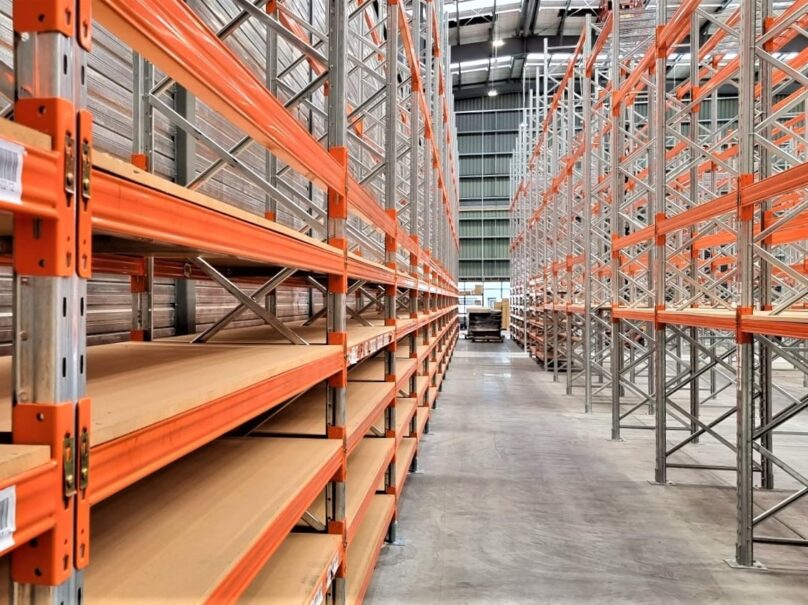
Now, let us take a look at the reasons why warehouse racking matters so much.
1. Maximizing Storage Capacity
Warehouse space often comes at a premium.
A well-designed racking system allows for vertical expansion of storage capacity without increasing the physical footprint of the warehouse.
Storing upwards, instead of just outwards, enables businesses to take full advantage of ceiling height.
- Optimizes cubic space
- Reduces need for off-site storage
- Minimizes congestion on the warehouse floor
2. Improving Accessibility and Organisation
Time is a critical factor in logistics. A racking system that aligns with product flow and warehouse layout improves the ease of access for staff using forklifts or manual picking methods.
Proper organization directly improves picking speed and order accuracy.
- Makes product identification faster
- Supports inventory rotation strategies
- Reduces time lost to searching for misplaced goods
3. Enhancing Safety
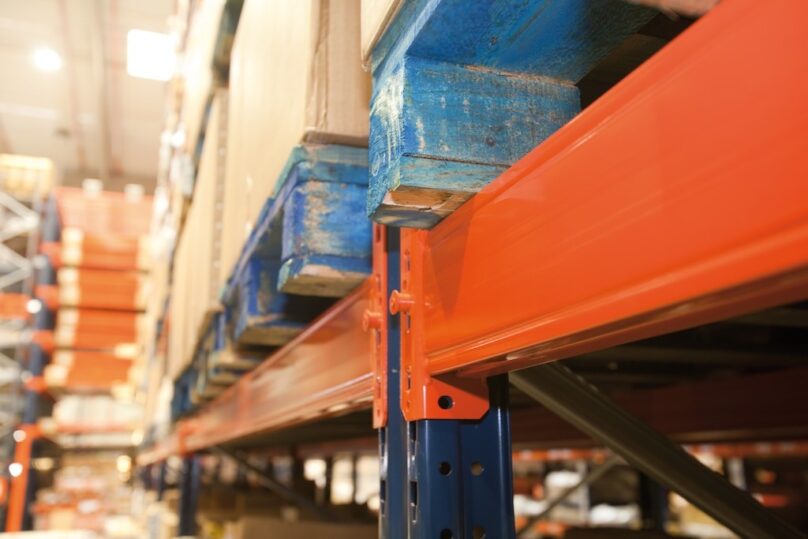
Racking that meets safety standards reduces the chance of collapses, falling products, or load shifting.
Regular inspection and proper installation are essential for maintaining a hazard-free workspace.
- Prevents structural failures
- Reduces risk of injury
- Complies with workplace safety regulations
4. Supporting Scalability
As operations expand, modular racking systems can be adjusted, relocated, or extended.
This makes it easier to adapt storage to new product lines or increased volumes without redesigning the entire warehouse.
- Modular and adjustable components
- Fits evolving logistics needs
- Supports automation upgrades
Common Types of Warehouse Racking
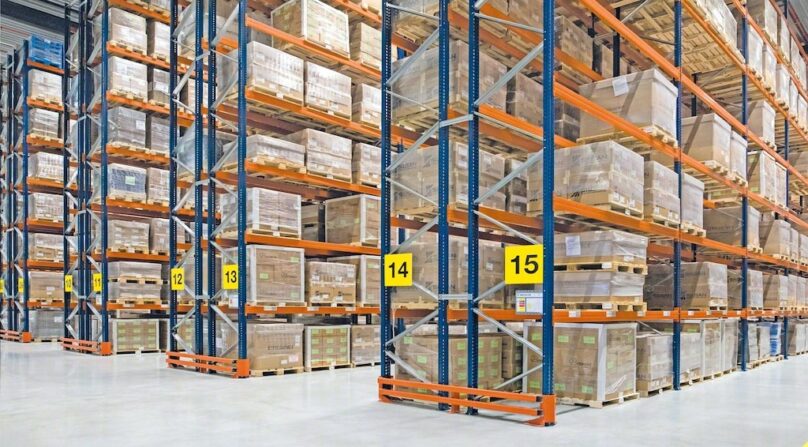
The most effective racking system depends on inventory types, handling frequency, and available warehouse infrastructure. Here are the most widely adopted systems:
Selective Pallet
Ideal for operations requiring direct access to each pallet.
Offers great visibility and accessibility, making it suitable for a wide range of products.
- Single-deep configuration
- Simple to install and reconfigure
- Compatible with most forklifts
Drive-In / Drive-Through
Best for high-density storage with limited product variety.
Drive-in setups follow a Last-In-First-Out flow, while drive-through systems enable First-In-First-Out rotation.
- Reduces aisle space
- Maximizes volume for uniform goods
- Requires careful driver operation
Push-Back
A dynamic system where pallets rest on wheeled carts that move along inclined rails.
When a new pallet is loaded, the existing ones are pushed back.
- Increases storage density
- Provides selective access compared to drive-in
- Suitable for medium-turnover items
Cantilever
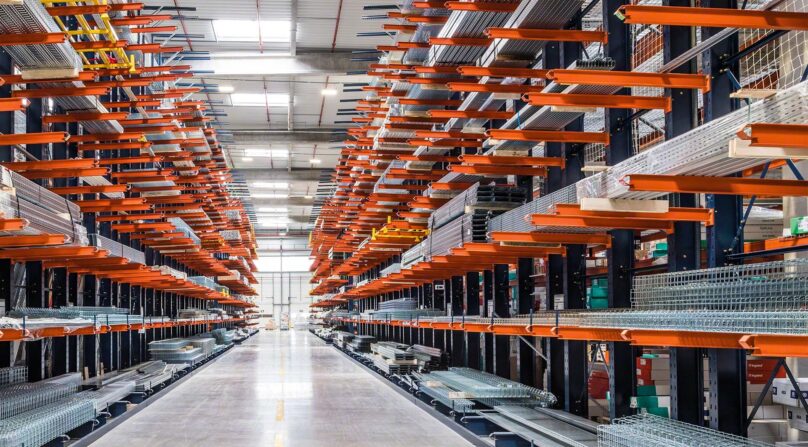
Specifically made for long, bulky items that won’t fit in traditional pallet spaces, such as steel rods, timber, or piping.
- Open-front design
- Adjustable arms for various lengths
- Perfect for materials that cannot be palletized
Mezzanine
Adds a second level of storage or workspace, effectively doubling usable space in high-ceiling warehouses.
- Creates new zones without structural expansion
- Supports shelving or office areas
- Ideal for rapidly growing operations
Choosing the Right Warehouse Racking System
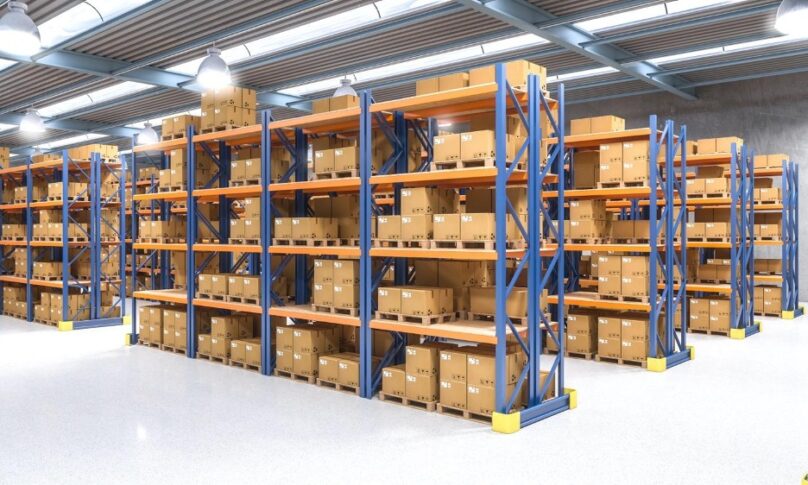
Selecting the correct warehouse racking system is a strategic decision that directly influences storage efficiency, workflow productivity, and long-term scalability.
The right choice depends on more than just how much can be stored. It should reflect the nature of your inventory, how your team operates, and the technical constraints of the facility.
A poorly matched racking setup can lead to traffic bottlenecks, inventory mismanagement, or even safety hazards. To avoid these pitfalls, consider the following key factors:
Inventory Type and Volume
Start by analyzing what you store and how much of it. Racking systems must accommodate your inventory’s physical characteristics:
- Palletized goods may require selective or push-back systems.
- Loose or irregularly shaped items may fit better on cantilever or bin shelving.
- Heavy-duty items might demand reinforced frames and beam capacities.
Choosing a system that matches the size, shape, and weight of your inventory prevents damage and makes storage more efficient.
Turnover Rate
The frequency at which products are picked, restocked, or rotated should influence the design.
High-turnover items benefit from easy access, while slow-moving goods can be stored deeper or higher up.
- Fast-moving SKUs should be placed in front-facing or lower-rack positions.
- Bulk storage of low-turnover items may use drive-in or double-deep racking.If FIFO rotation is important, drive-through or carton flow racks offer advantages.
Designing racking around turnover patterns shortens retrieval time and keeps labor costs in check.
Warehouse Layout
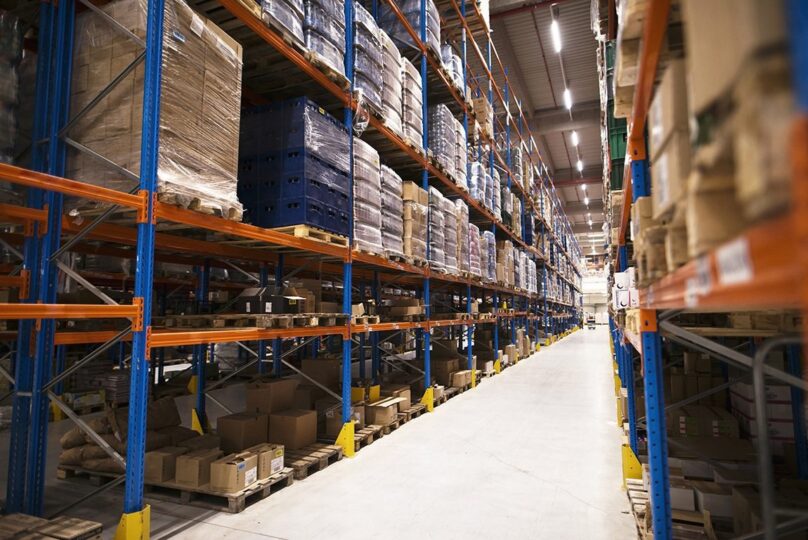
Every warehouse is constrained by its structural elements, ceiling height, column spacing, floor load limits, and fire safety codes.
Your racking system must fit within those boundaries without reducing accessibility.
- High ceilings allow for taller racking with more levels.
- Wide column spacing permits better aisle flow and forklift turning.
- Mezzanines or multi-level systems make better use of vertical space when floor area is imited.
Accounting for your layout early avoids expensive modifications later.
Handling Equipment
Different types of material handling equipment are compatible with specific setups.
The racking system must support efficient movement and maneuverability of your forklifts, pallet jacks, or reach trucks.
- Reach trucks require narrower aisles and deeper rack configurations.
- Standard forklifts need more aisle clearance but offer flexibility.
- Order pickers pair well with selective racking or carton flow systems.
Misaligning racking and equipment can lead to inefficiencies and damaged inventory.
Budget and Long-Term Needs
While some racking systems offer a lower initial cost, others provide better scalability or reduced maintenance over time.
Make sure your selection aligns with your business’s growth expectations and budgetary constraints.
- Modular systems can be expanded or reconfigured as needed.
- More robust systems might reduce replacement or repair costs.
- Cost should be evaluated over the full lifecycle of the system, not just installation.
Long-term planning reduces the need for costly overhauls as operations scale.
Consult a Warehouse Racking Specialist
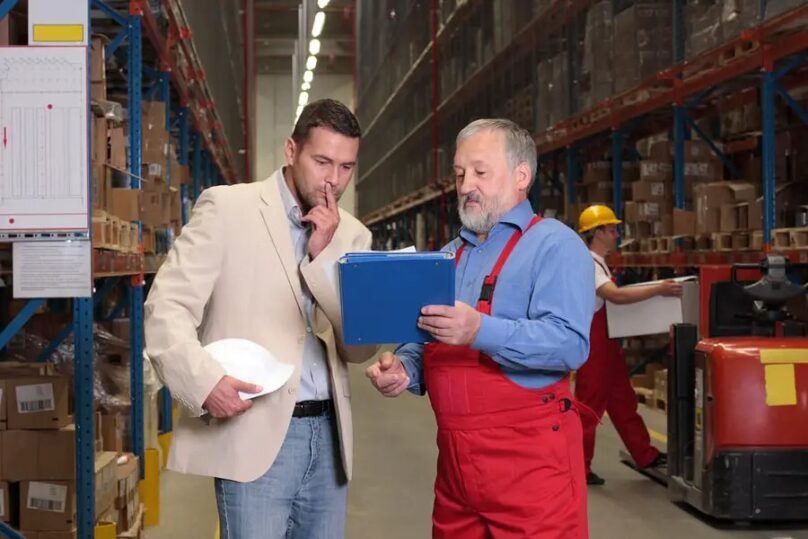
A professional warehouse planner or supplier brings technical insight and practical experience to the table. They can:
- Analyze workflow and product movement
- Identify the most efficient setup for your layout
- Ensure compliance with safety regulations
- Recommend solutions that accommodate current and future needs
Expert consultation leads to a system that not only fits your current operation but also supports future expansion and optimization.
Final Thoughts
Investing in the right warehouse racking system is more than just a space-saving solution—it’s a strategic decision that improves workflow, reduces costs, and supports long-term business growth. Whether you’re optimising a new facility or upgrading an outdated setup, racking is the framework that holds your entire operation together.
With proper planning, installation, and maintenance, warehouse racking can take your logistics to the next level—one pallet at a time.